
THIS SITE USES GOOGLE ANALYTICS TO ANALYSE TRAFFIC. CONTINUING TO USE THIS SITE MEANS YOU ACCEPT THE USE OF COOKIES. LEARN MORE OR SEE OUR PRIVACY POLICY
SEVEN DAY CYCLIST
CYCLING, BUT NOT USUALLY RACING
LATEST UPDATE: APRIL 22nd
HOW DO WE DECIDE OUR OVERALL RATINGS FOR PRODUCTS WE REVIEW?
RUB A DUD HUB
A step by step guide overhauling Shimano cup and cone freehubs
Rub a Dud Hub,
Michael's went THUD.
What do you think he did?
Well he serviced it, of course!
​
And this is what he did ......

Aside from regular cassette replacement, periodic cleaning and regreasing of its quick release skewer, this particular unit has soldiered on untouched for several seasons and 5,000miles. However, a ghoulish, gritty grumbling emanating from its inner sanctum confirmed serious TLC was in order.
​
For the uninitiated, Shimano’s six bolt, disc ready M475 freehub is a relatively inexpensive cup and cone model, closest in linage to Alivio but sharing some common parts with the Japanese giant’s more widely revered Deore. Nonetheless, servicing protocol is broadly identical for all three.
​
Simple labyrinth seals mean the 475 is best suited to commuting, touring and general road riding. Regardless of sophistication, sealed bearing components are designed to withstand the sort of water pressures experienced during shallow river crossings and gentle rinsing with garden hoses - not jet washing. Doing so simply forces water inside. With no means of escape, slowly but surely, this destructive element induces corrosion, seizure and ultimately catastrophic failure.
​
Look online and there’s a fair few forum commentators advocating replacement rather than overhaul of the lowlier ranges, arguing a new unit can be had for the same price as a shop strip. However, this doesn’t factor the cost implication of wheel re/building.
Tools
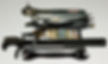
Chain Whip or Pedros “Vies Whip.
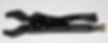
-
Cassette Lock-ring tool
-
10mm Allen Key (For removing freehub body)
-
15mm cone spanners
-
17mm ring spanner (for locknut)
-
Small flat bladed screwdriver (biro lids will work in a pinch)
-
Replacement Bearings ¼ inch 9 per side
-
Good quality e.g. Teflon/Ceramic/Polymer grease.
-
Clean Rag
-
Torque wrench (optional)
Approximate time required 30mins c. (£25 including parts and labour when undertaken by independent mechanic/retailer).
​
Step 1

Start by removing the quick release/security skewer. Clean these in biodegradable solvent, wipe dry and leave to one side for now. Next comes the cassette. Wrestle the cluster into submission using a chain whip (Pedro’s vise whip makes this task that bit easier), introduce the lock-ring removal tool and turn it counter clockwise with a long handled adjustable wrench. Stiff, high quality grease during fitment ensured ours relented with only moderate force.

Badly weathered examples may require judicious blasts of penetrating fluid such as Plus Gas-generic maintenance sprays can help in some cases but aren’t nearly so effective. Having slipped the cassette free, maintain correct sprocket spacer sequence by threading everything together using a zip tie. Leave oily, congealed examples marinating in biodegradable degreaser (old ice cream tubs make worthy substitutes for parts washers). Theoretically the cassette system means individual sprockets are easily and cheaply replaced when worn but in reality, a fresh cluster (and chain) can prove better economics.
​
Step 2

With clear access to the locknut and cone assemblies, we turn our attentions to the left (non-drive) side. Pop that 17mm ring spanner on the locknut (turning counter-clockwise) while engaging the 15mm cone wrench clockwise.

Up close and personal, it appears the freehub body has sheared, so needs replacing. Fortunately, we’ve a healthy donor deore unit salvaged from an irreparably bent wheel. Access to the right hand bearings necessitates removal in any case.
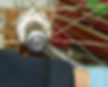
Slide a 10mm Allen key until it locates within the recessed bolt and then turn counter clockwise. This is easiest with a long-handled ratchet, although T handled types are generally up to the job. Again; a liberal blast of penetrant spray makes the whole process much smoother, avoiding frayed tempers, grazed knuckles and agricultural outbursts.
Step 3

Remove locknut, spacers and cone from the axle, observing order before judiciously slipping the axle free from the other side. In this instance the resident bearings are shot, so it doesn’t matter but placing a rag beneath the hub during routine inspections prevents ball bearings scattering lemming-fashion beneath fridges, benches and other inaccessible regions.
Step 4

Gently tease the bearings free using a small screwdriver or similar implement, taking care to avoid scoring the hub shells or gouging the seals.
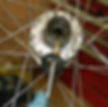
Now clean the races with some clean rag dipped in solvent, checking for any signs of pitting or cracking. Similar housekeeping is needed at the hub shell’s splines.

Assuming this region is sound, introduce a measured quantity of Teflon/ceramic or polymer grease here and to the freehub retaining bolt before reinstating.


Step 5
​
Before adding a fresh bed of grease to the hub shells, roll the axle across a flat surface.

Wobbling indicates its bent and requires replacement. Ours runs true, so is repatriated once we’ve installed new bearings.

As with any component, these also come in different grades. Lower numbers denote better quality and more accurate machining.
​
Higher end Shimano groups use 40 and sometimes 25 grade, which cost around £9 for a pack of 50 (Enough for several rebuilds). However, in this instance (Or indeed more prestigious models relegated to workhorse duties) 100 grade are more than adequate and approximately half the price. Starting at the drive side, introduce those new balls, guiding them home with a flat screwdriver/tooth pick as necessary.
​
Thread, the cone aboard the axle’s non-drive side and slide through the hub shell. Repeat and then slide everything in situ.

Nip the cones snug, and spin while holding the wheel vertically to assess bearing tension - this bit requires practice. Once everything turns smoothly, reintroduce spacers and locknut. Holding the cone still with that 15mm spanner, tighten the locknut against it.
Step 6
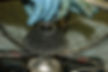
Satisfied everything’s buttery smooth, slot the cassette aboard the freehub, add a slither of grease to the lockring and tighten firmly - to 30n-m if using a torque wrench.

All that remains is to add the skewer, remount and you’re ready for another year’s faithful service.​
With thanks to Alan at Riverside Cycle Centre for his assistance. www.riversidecyclecentre.co.uk
PUBLISHED DECEMBER 2016