
THIS SITE USES GOOGLE ANALYTICS TO ANALYSE TRAFFIC. CONTINUING TO USE THIS SITE MEANS YOU ACCEPT THE USE OF COOKIES.WE DO NOT COLLECT PERSONAL DATA LEARN MORE OR SEE OUR PRIVACY POLICY
SEVEN DAY CYCLIST
CYCLING, BUT NOT USUALLY RACING
LATEST UPDATE JULY 23rd
HOW DO WE REACH THE OVERALL RATINGS FOR PRODUCTS WE REVIEW?
RUBBER FETISH: TALKING TYRES
Michael Stenning gets a grip on tyres for commuting and everyday cycling.
Just as the best bike is that which performs its intended purpose with no, or minimal compromise; tyre choice isn’t an exact science. At one extreme, riders combining training and commuting may prioritise fast over puncture resistance. Others may want bombproof sidewalls/casings and shrug at the thought of adding 2,000g to their wheels. Obviously, there are several shades in between, although certain characteristics are particularly desirable when choosing everyday tyres.
Tread Patterns
​
Treads might be psychologically reassuring. However, they won’t bite into the road’s surface. MTB knobblies are prime examples, squirming and losing contact when cornering hard - especially over wet manhole covers and similar ironworks.
​
Cars and larger vehicles need tread because their tyres sit square and the leading edge runs in a straight line, trapping water and impairing traction, especially at speed. Bicycles have curved road contact, requiring a rounded contact area. This combined with much higher pressures tends to force water aside.
Therefore, completely slick, soft compounds such as Schwalbe’s aptly named Kojak and Freedom "thickslick" offer maximum contact over metalled roads. However, they are more susceptible to cuts/sharps and will wear quicker than harder compounds.
​
Weekly inspections and a quick drop of super glue into superficial wounds keeps anything nasty in check.



Manufacturers responded to this aversion with dual compound models such as Vittoria Street runner, which combine a harder centre strip and softer shoulders. Theoretically, these improve durability without impairing efficiency. Just as slicks should never be confused with a bald tyre, dual compounds are entirely different from dire “dual purpose” designs that swept in with mountain biking’s first wave.
​
Immaterial on a genuine slick, obviously but contemporary tyres are sometimes front/rear specific and sidewalls usually feature directional arrows. Ignoring the latter commonly results in skittish, unpredictable and potentially dangerous handling-especially in wet, slippery conditions.

Rolling Resistance
Simply put, the less rolling resistance, the more efficiently a tyre will convert rider effort into forward motion. Aside from choice of rubber compound and minimal tread, thin sidewalls, high TPI (Threads per Inch) width and indeed diameter are significant factors.
​
Smaller tyres accelerate quicker and wider tyres can be more efficient at lower pressures. It was once believed narrower tyres were faster by default. However, if a broader tyre is made of identical materials and thickness, it will roll more quickly.
​
This is due to lower internal friction and surface imperfections being more easily absorbed by the tyre. Therefore, 23mm will roll faster than a comparable 20mm and explains 23mm’s dominance over narrower section in competitive road riding/racing contexts, though, even here, some are taking to slightly broader tyres.
​
Threads per Inch (TPI)
Tyres are not constructed from rubber, but from nylon or cotton covered in rubber. TPI refers to the number of nylon strands and ranges from 20 to a whopping 330. Most manufacturers provide this data on their websites and often the sales tag. Loosely speaking, bigger numbers denote a lighter, more compliant ride thanks to more thread and less casing.
​
That said; popping a 300 TPI tyre on a single brake fixer build and expecting it to withstand skid-stopping is asking for serious trouble! Not so long ago, 120 TPI was the preserve of race rubber but is becoming increasingly typical on higher end commu-touring models. 60 TPI indicates a tough winter/commuter tyre that will handle inclement roads and moderate loads, while still delivering a fairly zippy, responsive ride.
Sidewalls
These define a tyre’s structural integrity and come in two basic varieties. “Skin Walls” are characterised by a rubber layer thin enough so the threads are clearly visible. Ride quality is rewarding but these are more susceptible to cuts and similar structural woes - not ideal for crashing through potholes or hopping kerbs.
​
“Gum walls” are much thicker and often feature practicalities like Scotchlite reflectives and dynamo tracks for good connectivity with bottle units; an obvious choice for heavy touring and slogging through winter’s worst.

Correct width
​
Despite increasing standardisation, some come up smaller than others. Not overly problematic for a standard XC mountain bike rim but measure the width carefully if you’re experimenting. This harks back to the 1980s when cut throat competition between manufacturers led to some marketing theirs as a 23/25/28mm when they were in fact 21.5, 24, 27mm etc.
Sneaky practice which enabled rival brands to claim advantage on the scales and another good reason for measuring wheel size and circumference manually (rather than relying on pre-sets) when calibrating bar mounted computers.
Rule of thumb suggests that a tyre should not exceed 220% of a rim’s total width. So, one measuring 17mm will safely entertain anything between 23 and 37mm. Go narrower and expect harsh ride/potential rim damage, bigger invites the tyre to squirm form the rim, calliper or V- brake pads may rub the sidewalls, causing unnecessary heat build-up when descending.
​
Handling can turn seriously hairy too should a blowout strike. I can attest to this first hand having popped a 2.3 inch rear tyre on my trail hack. This was back in 1990 when mountain bike rims were beginning to get thinner; derailleur cages hung a hairs breadth from terra firma and 1.75-2 inch section knobblies were fairly mainstream.
​
Determined to crack 30mph along two miles of almost deserted dirt road, I’d just clicked up to the big ring when the sidewall exploded, blowing me sideways, bush bound and interrupting an amorous couple. To this day, I’m not sure who was more surprised.
Along with frame clearances, mudguards should also be factored into the equation.
​
These black chrome plastics are reckoned big enough for 45mm section tyres. In practice, anything larger than a 37mm slick (or deep tread 35mm) tickles the sides. Sometimes, localised contact can be cured by judiciously flattening that section of mudguard but proceed cautiously….
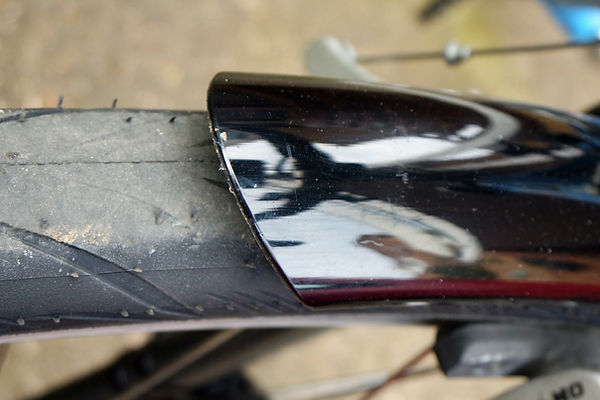
Puncture resistance
​
Kevlar, synonymous with bulletproof vests remains the standard by which all puncture repelling strips were judged. Be wary of confusing bead with belt. Kevlar beads are designed for convenient folding and low weight. Belts protect against flats.
​
I use a colossal wand-type workshop lever at home, which makes short work of the most difficult customers. That said; it’s not something you’d want bounding round in a pannier, or taped beneath your top tube. Consider ease of removal/fitting using those short, stubby resin types.
Talking of which no tyre (aside from “solid” designs) is completely puncture proof so give some consideration to fitting, invest in a track pump (Integral units have become much better but a standalone gauge is a wise investment) and run at the pressures denoted on their sidewalls.
​
Frequent flats in belted tyres indicate something is very wrong. Often these strike once the casing has worn beyond a certain point, though inspect rims for splits in their sidewalls, protruding spokes and/or wandering rim tapes (Those with adhesive backings are best - there’s no risk of them slipping and exposing spoke heads).
​
There was a misguided trend for alternating front/rear tyres for even/optimal wear. Worn rubber on the front end is begging for a blowout and potentially very serious, if not fatal injury. We can all appreciate the lure of saving a few quid. Therefore, if your rear’s seen better days, swap it for the front and replace that one for something factory fresh.
Often regarded as outclassed by Aramid and similar yarns (although these are both of the same polyamide family) the quest for alternatives boils down to cost. Kevlar is both expensive and dangerous to manufacture.
Many tyres simply feature a centre-strip, which is pretty effective, though leaves shoulders and sidewalls vulnerable to glass, thorns, flints and similar damage. Bead to bead is more dependable. Some brands engineer their casings with a thicker rubber which actively deflects sharps.
​
Schwalbe Smart Guard employs a 5mm inner barrier, which is designed so a really sharp tack cannot penetrate, causing a puncture. This has some implications for weight and rolling resistance but I’ve found them extremely reliable.

CLICK ON THE PICTURE FOR TYRE REVIEWS
PUBLISHED ON THIS WEBSITE NOVEMBER 2016