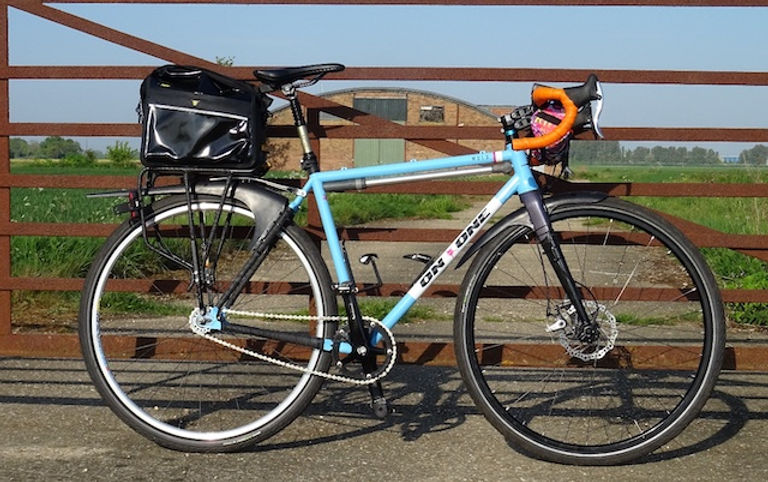
THIS SITE USES GOOGLE ANALYTICS TO ANALYSE TRAFFIC. CONTINUING TO USE THIS SITE MEANS YOU ACCEPT THE USE OF COOKIES.WE DO NOT COLLECT PERSONAL DATA LEARN MORE OR SEE OUR PRIVACY POLICY
SEVEN DAY CYCLIST
CYCLING, BUT NOT USUALLY RACING
LATEST UPDATE AUGUST 18th.
HOW DO WE REACH THE OVERALL RATINGS FOR PRODUCTS WE REVIEW?
POST MODERNISM
These days contact points, seat posts in particular, fall into three, sometimes four diameters. Most “quality” bikes use 27.2, 30.9 or 31.6. This lowers costs for manufacturers and ultimately means, carbon and other cutting edge materials are pretty affordable. Upgrading is usually straightforward, so long as you have the correct diameter but older frames can present some unexpected challenges. Michael Stenning confronts seat-post modernisation.

27.2mm has always been a popular diameter - my 531 1955 Holdsworth being a case in point. In this instance, aside from checking the seat tube has been properly cleaned out and there’s no corrosion/structural damage lurking inside, Ti, Carbon, high end aluminium alloys… You’re only limited by your budget.
​
Some production bikes from the late 1980s boasted very high spec with seriously enticing price tags. Sometimes a complete bike could be had for the price of a groupset. Cheap headsets and bottom brackets were cheeky, but the norm and easily hidden.
However, a sometimeish attitude to detailing meant seat tubes weren’t reamed properly, ruining a pretty post. Good dealers would sort this beforehand, or worse case scenario, under warranty, but its worth getting this sort of stuff checked, especially if you’ve just bought a classic frame for Eroica-like events.
Urban Myths
​
Be wary of falling into the trap of thinking all better-quality frames were 27.2. While a popular size and it was commonly accepted that larger diameter and better frame quality went hand in hand, plenty, including 1970s ALAN, came in at 25.0 or 26.0 upward in .2 increments.
​
This remained popular through the 70s, 80s and 90s, especially during the mountain bike boom. Some production tandems, including Dawes’ Galaxy were 27.0. During this period, in an attempt to compete with increasingly sophisticated tubing, thinner walled versions of old favourites were also 27.0.
​
Checking the Size
​
Assuming the frame in question already has a post in situ, the sizing should be etched into the base.


No? Measure it with a digital Vernier.
​
Hell, measure it anyway, since price still influences precision. Right royally stuck? Take a look at our guide to shifting seized contact points.
No post? Assuming you already know the frame’s identity, take a wander round the web. These days you’ll find reputable sites listing production frames and their specifications. I’ve taken this particular route in the past and got lucky. However, returning something that doesn’t fit is a faff and a retailer is unlikely to give refunds on a scratched; or otherwise damaged contact point.
​
A better option is trying a few spare posts of different sizes that might be lying around in friends’ spares drawers.
​
Better still; give your friendly independent bike shop/frame builder a call. If the frame’s new to you, ask them to double check condition of the seat tube and re-ream if required, say, following a re-spray.
​
Chances are they’ll also have a post rod. This works like a jeweller’s ring pole and have diameters engraved on the side. Fed inside the seat tube, once it fits flush, you have the correct size.

Reaming the Frame
​
Ok, so you’ve sizing sussed but this restricts your choices. For the most part, 6061 or 7005 posts made in the Far East are plenty light enough, reasonably finished and ultra-reliable. Ah but you fancy something flashier, carbon perhaps?
An experienced frame builder may be open to increasing the seat tube’s diameter by a very small increment, say .2mm. However, 4130 and other steel alloys are surprisingly tough and even removing this tiny amount of metal is hard going. Similarly, if they say removing anything will affect the frame structurally, take note.
​
Never attempt to talk them into it, or having a go yourself! Justin Burls http://www.burls.co.uk/bicycles.php agreed to do some post re-spray prep on a favourite frame of mine dating back to 1991. However, he declined to remove any more metal, even though the frame was A1 internally, since he feared this would be enough to induce failure.
Machine shops
​
If reaming the frame out is a no-no, or you’ve scratched a nice metal post, having guestimated its diameter, don’t panic. A machine shop may be able to reduce the post's diameter using a metalworking lathe. This may result in some light swirling/marks. Fine if these are hidden inside the frame and you could always have the exposed section painted or powder coated.
​
Layback designs, including this Thomson are less straightforward. A local engineering firm were initially quite willing, but refused on the basis it wasn’t straight. In this instance, there was at least 12cm of post going inside the frame. Armed with digital calliper and emery paper, I sanded the section by hand down from 27.2 to 27.0, checking regularly to avoid mistake.

DISCLAIMER
​
THIS AND SIMILAR MODIFICATIONS DISCUSSED HERE WILL INVALIDATE ANY WARRANTEE. THE FOLLOWING PROCEDURE WAS PERFORMED AT MICHAEL’S OWN RISK, CONSULTING EXPERT OPINION.
SOLICIT THE ADVICE AND SERVICES OF AN EXPERIENCED AND QUALIFIED SHOP MECHANIC, FRAME BUILDER AND/OR ENGINEER BEFORE COMMENCING WORK OF THIS KIND.
​
NEVER ATTEMPT TO REDUCE THE DIAMETER, OR OTHERWISE MODIFY A CARBON/COMPOSITE COMPONENT.
Project Univega
Any refurbishment means minor imperfections stand out like a massive zit.
Though worthy and otherwise ultra-dependable, the Univega’s BBB skyscraper post’s dun finish was starting to look tired in places.

I toyed with the idea of upgrading to a Cane Creek Thud Buster ST, which are still readily available in 26.6 and a wealth of diameters popular on mid 90s mountain bikes. However, though well made and relatively low maintenance, weight and additional complication had me looking elsewhere.
Bodge Box Bounty
This plain looking Chinese, online auction site special was holidaying in my spares drawer. Titanium has a reputation for being difficult to extract and machine. However, this one proved a lot simpler to reduce than commonly assumed.
I began this project looking for a machine shop, so dropped John Moss an email, asking if he could recommend one. This immediately ignited his curiosity and he’d just bought a Clarke lathe ...
Some meticulous calculations later and he was confident he could take it from 27.2 to 26.0 at select points without compromising its strength/integrity.


Stage 1
​
Schooled in the measure twice, cut once school of engineering, rather than relying on folklore and misinformation, John set about researching titanium’s specific characteristics. He concluded that because titanium work hardens much faster than stainless steel during the cutting phase, once started he was fully committed - no margin for error; or pausing for thought!

Stage 2
​
Next, given the forces involved, John needed a method of bracing the post, keeping it firmly in place. The aptly named “fixed steady” https://www.machinemart.co.uk/p/fixed-steady-2/ would do this. Instead, John finds some leftover aluminium tube from the seat section of his Sinner Mango velomobile. A brace from the other end was created by boring a 30 degree aluminium alloy cone, inserted into the opposite end of the seat post.
Stage 3
​
With everything set up carefully on the lathe, John made three cuts in total and the whole reduction took an hour to achieve. I was surprised by the amount of titanium swarf (or chips in shop-speak). Unlike stainless steel, which can peel away quite violently, the Titanium came away in much smaller, predictable quantities
Titanium dust is toxic if inhaled, so any grinding or similar finishing process should be performed wearing a suitable mask. Despite his care and meticulous precision, some superficial swirling remained. Decreasing grades of wet and dry paper were polished out to achieve the finish you see here.
​
Cosmetics
​
I had toyed with the idea of having the post painted to coordinate with the Univega’s two-tone cream and black livery. Graham at Maldon Shot Blasting & Powder Coating http://www.ctc-powder-coating.co.uk/ said he would be happy to give it a satin black makeover. Since blasting was a non-starter, an etch primer would be applied to give the powder coat something to key to. However, titanium’s naturally corrosion resistant and alluring colour is extremely practical, so I’m leaving it raw, for now...


Fit
​
No surprise that it fitted the frame perfectly. Always apply some grease, or in the case of carbon, anti seize. Ti specific preps aren’t essential-I opted for a high quality PTFE paste and wound the binder bolt to 5nm. A month and over 400 mixed terrain miles, no problems, although I removed and inspected weekly to check for any signs of fatigue. Though wall thickness is thin at the base, we’re not talking wafer and I have run high end aluminium models of similar (stock) diameter long term and trouble-free.
PUBLISHED APRIL 2017
